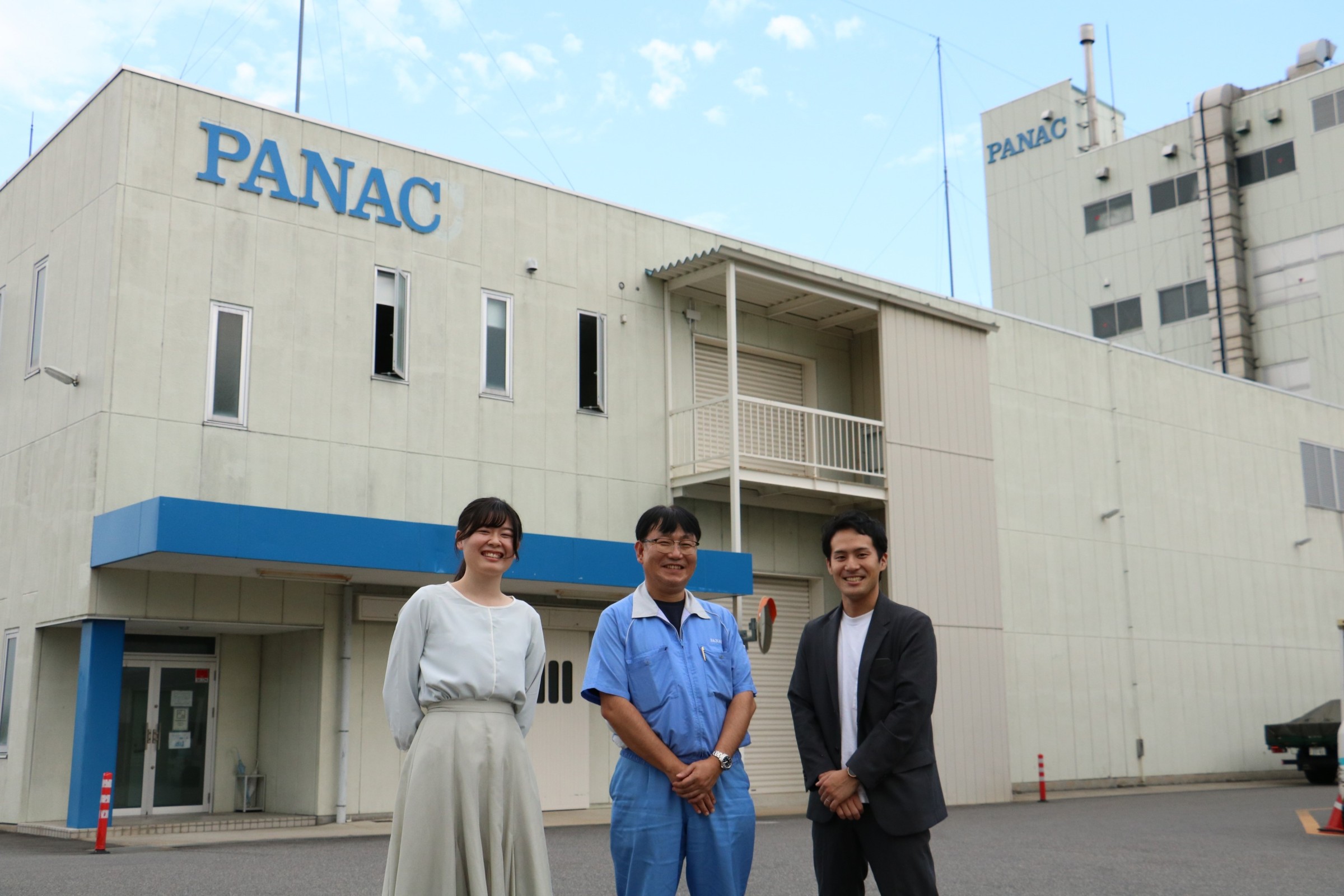
パナック株式会社様の亀山工場では、メーカー各社の各種高機能プラスチックフィルムを、工業材料、電子材料として加工しています。
工場では特に厳しい温度管理が必要な素材を扱っているのですが、事業が拡大するにあたり生産増と共に扱う材料も増えたことで、管理をデジタル化することが急務となっていました。工程のデータを正確に収集することで管理を効率化させるため、また顧客の信頼を守るために、加工工程の管理システムを導入。
素材の加工工程の管理について、システム導入の経緯や導入後の様子、管理の先にある大切な想いについてお話をうかがいました。
お客様:パナック株式会社 山口貴之 様
(担当:スノーピークビジネスソリューションズ GIS事業部 水口聡基)
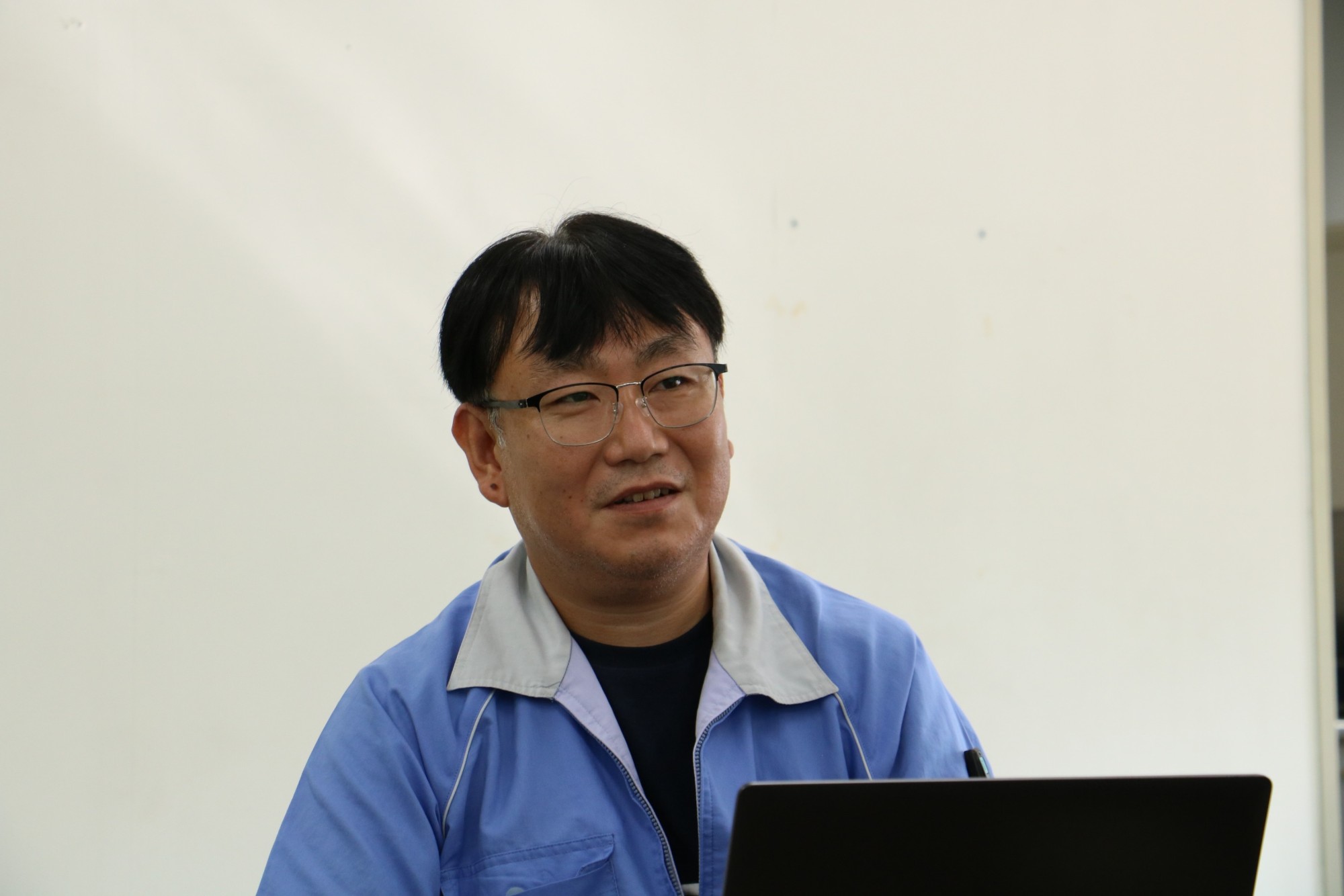
デジタル製品の進化にあわせ常に新しい機能性フィルムを提供
---パナックさんの事業概要について教えてください。
弊社は1933年に「中村玩具店」として創業しました。1979年に現在のパナック株式会社を設立し、機能性フィルムの商社機能とメーカー機能を兼ね備えた会社となりました。プラスチックフィルムにさまざまな機能を付けて、お客様へ提供しています。
弊社はフィルム素材を数ある種類の中から[探索]し、最適な形状に[加工]を施し、さらには新たな機能設計を[開発]しながら、安定した[供給]を行う、この4つの機能を自社で一貫対応ができることを強みとして、特徴ある企業に成長してきました。
亀山工場では、さまざまなフィルムを取扱う中、特に多くを占めているのが、ディスプレイやタッチパネル製品などに広く採用されている機能性フィルムの加工です。身近なものだとパソコンやスマートフォンなどに使用され、年々デジタル製品が進化するにつれフィルムも多様に進化しています。
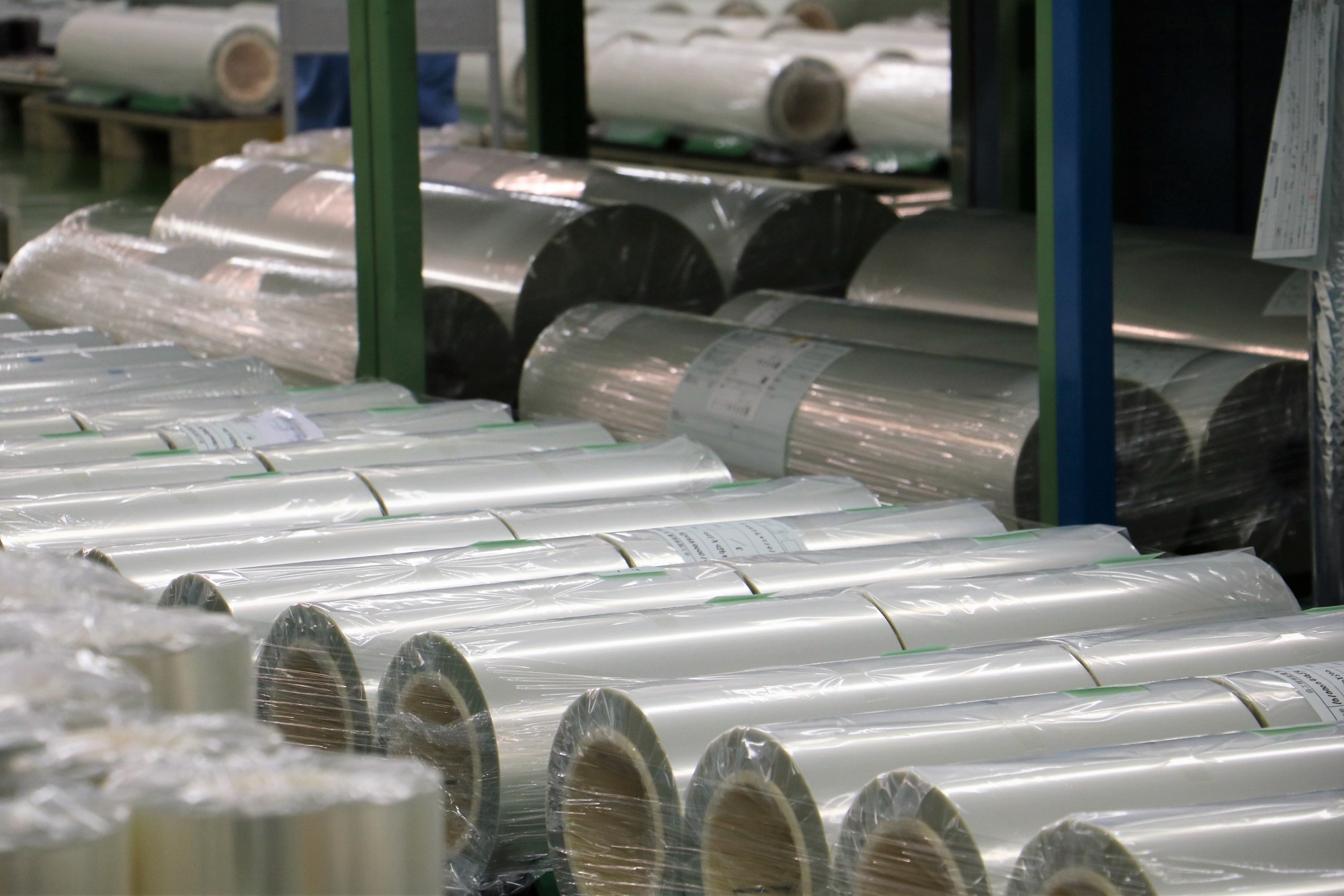
事業拡大を見越し、お客様の信頼を守るためにデジタル化を決断
---工程管理システムの導入を検討した背景は?
検討を始めたのは2019年ごろでした。当時新しく取扱うことになった部材は、今まで取扱っていた部材と違って冷蔵保管が必要なもので、倉庫から出庫して加工する間の常温におかれる時間を管理する必要が出てきたのです。初めは取扱い数が少量だったこともあり、アナログの台帳で管理をしていました。
しかし取扱い商品が増えるにつれ、お客様側からロットごとに細かく管理をして、「記録を残しておいて欲しい」「エビデンスが出せる状態にして欲しい」という要望があがってきました。アナログの管理だと、どうしてもスタッフによって正確さにばらつきが出てしまいますし、お客様から過去の工程について確認された時には、当時担当していたスタッフの記憶に頼るしかない状態でした。
今後この部材の商流が増えていく可能性を見越して、管理をデジタル化することがお客様への信頼と他社との差別化につながると思い、システム管理を決断しました。
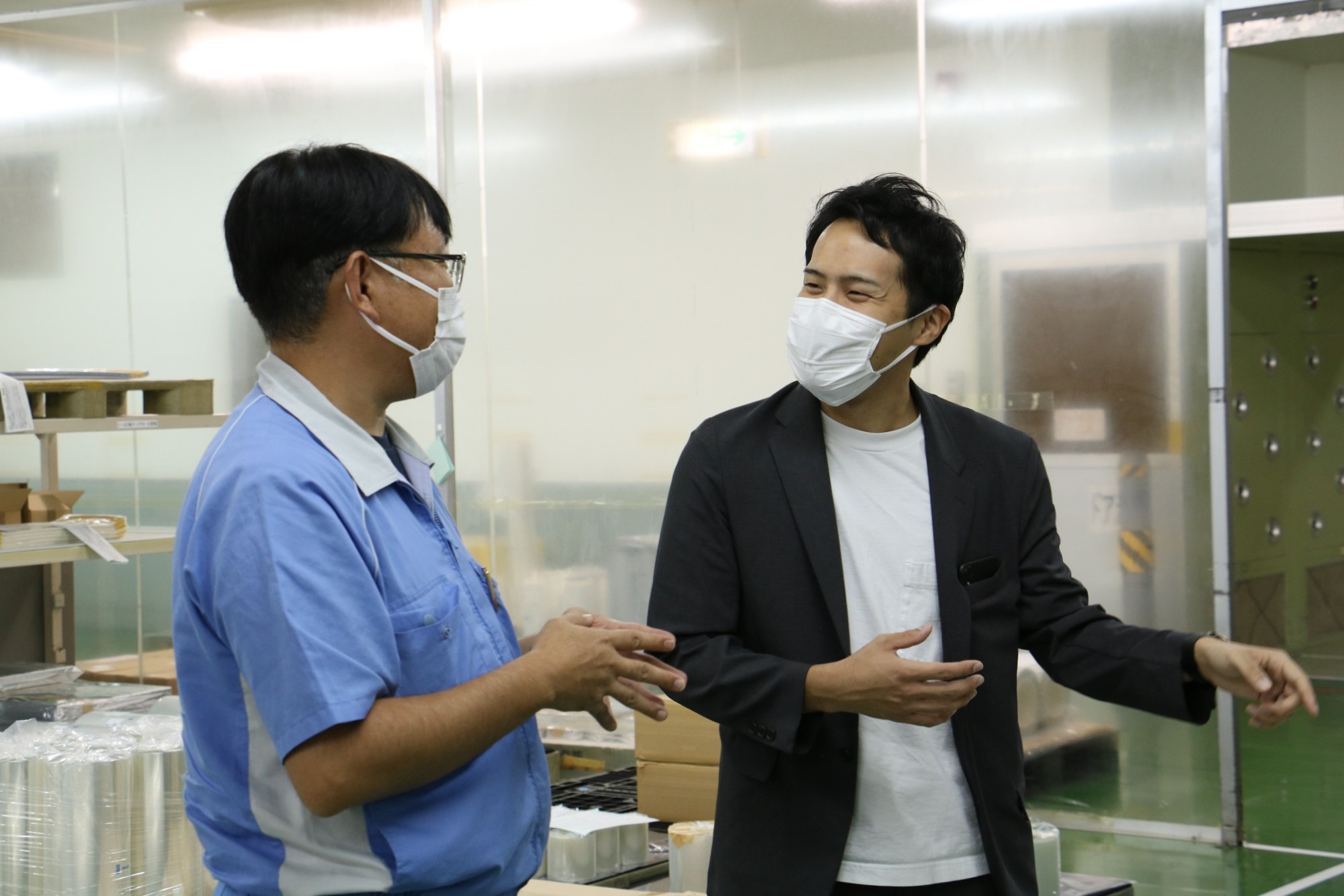
共に理想をカタチにできる安心感とスピード感
---スノーピークビジネスソリューションズ(当時、ハーティスシステムアンドコンサルティング 以下、SPBS)のシステムを選ばれた決め手は何だったのでしょうか?
システムを導入するまでのリミットが半年という中、「納期」と「パッケージではない現場に合わせたシステム」を重要視してシステム会社を探していました。インターネット検索で初めにヒットしたのがSPBSです。
問合せ後すぐにヒアリングと現場見学に来ていただけて、工場のある三重県亀山市と愛知県岡崎市という距離の近さにメリットを感じました。短い納期の中でタイムリーにやり取りできることがとても重要なアドバンテージだったので、レスポンスの早さは大きな決め手だったと思います。
また、手短に要点をつかんでもらえる企業に依頼したいと思っていたところ、こちらが「こんなことがやりたい」と話したことをすぐに図解し、イメージに起こして見せてくれたのです。イメージをもとにお互いの認識を合わせながら話し合うことができましたし、提案書にはこちらの要件や意図していることがしっかりと汲まれていました。理解力と弊社との相性の良さからも、ここなら安心して任せられると感じました。
早くから工場長も交えて打合せをしていたこともあり、やりとりがスムーズに進みすぐに承認を得ることができたのです。
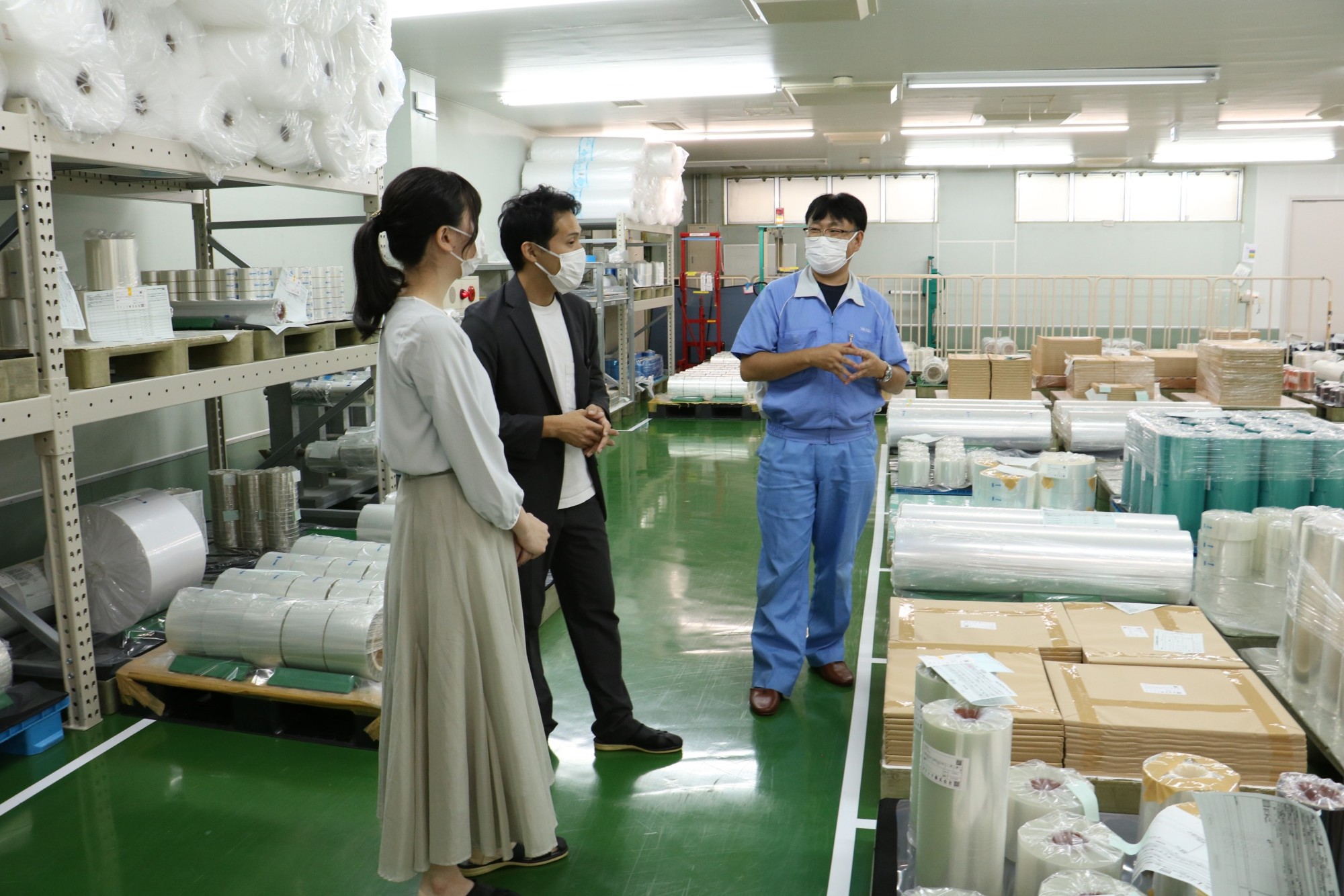
まずはシンプルに。そしてテンポよく。
---短期間でのシステム導入でしたが、うまくいったポイントはどこでしょうか?
「コミュニケーション」と「シンプルに始める」という2つの要素がうまくいったポイントだと思います。
まず、導入を決めてからも現場検証や情報のやり取りはこまめに行い、テンポよくシステム開発を進めてもらえたところです。こちらの要件が複雑ではなかったこともありますが、最初の段階ですり合わせがしっかり行えていたことも大きいです。
そして、「まずはシンプルに初めステップを踏んでシステムを現場に合わせていく」という、SPBSさんの基本方針が私たちの想いとマッチしていたことです。最終的に理想とする完成形と納期とのバランスをとり、3ステップに分けたシステム導入を提案してもらいました。まず最低限必要な機能は何か、その上でよりパフォーマンスを上げられることは何か、ということを一緒に現場を見ながら考え少しずつ仕上げていきました。
ステップ1では、入庫した素材にラベル貼付を行い、入庫から出庫までの亀山工場に保管されている時間を取得できるようにし 、ステップ2では、冷蔵庫から出して加工されるまでの時間を各行程ごとに記録できるようにします。そして最終ステップでは、他拠点でも同じシステムを導入し、各拠点の保管時間を亀山工場で一括管理するという構想です。最初に亀山工場でトライアルを重ねたことで、他拠点でも同じレベルで管理ができるようになりました。
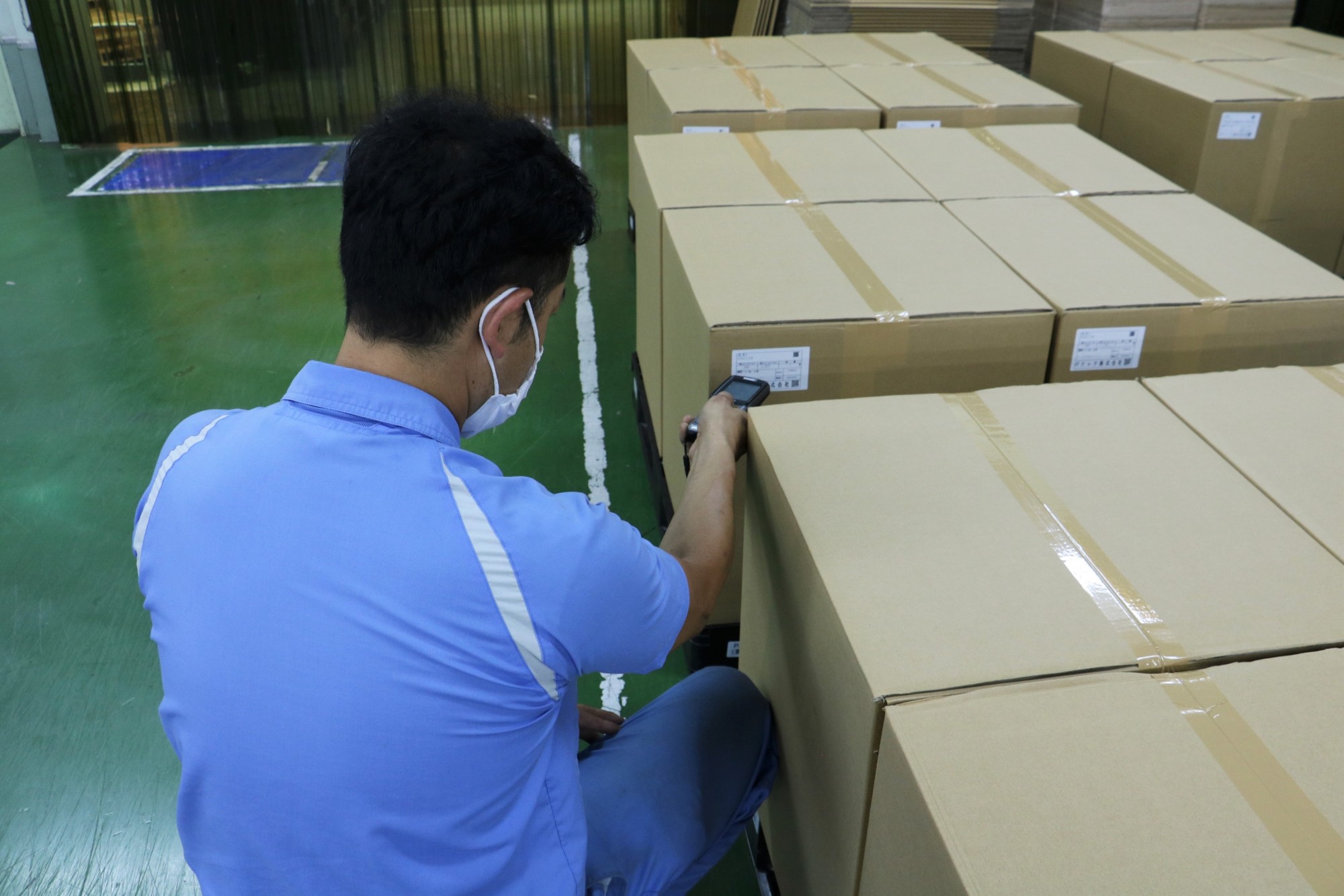
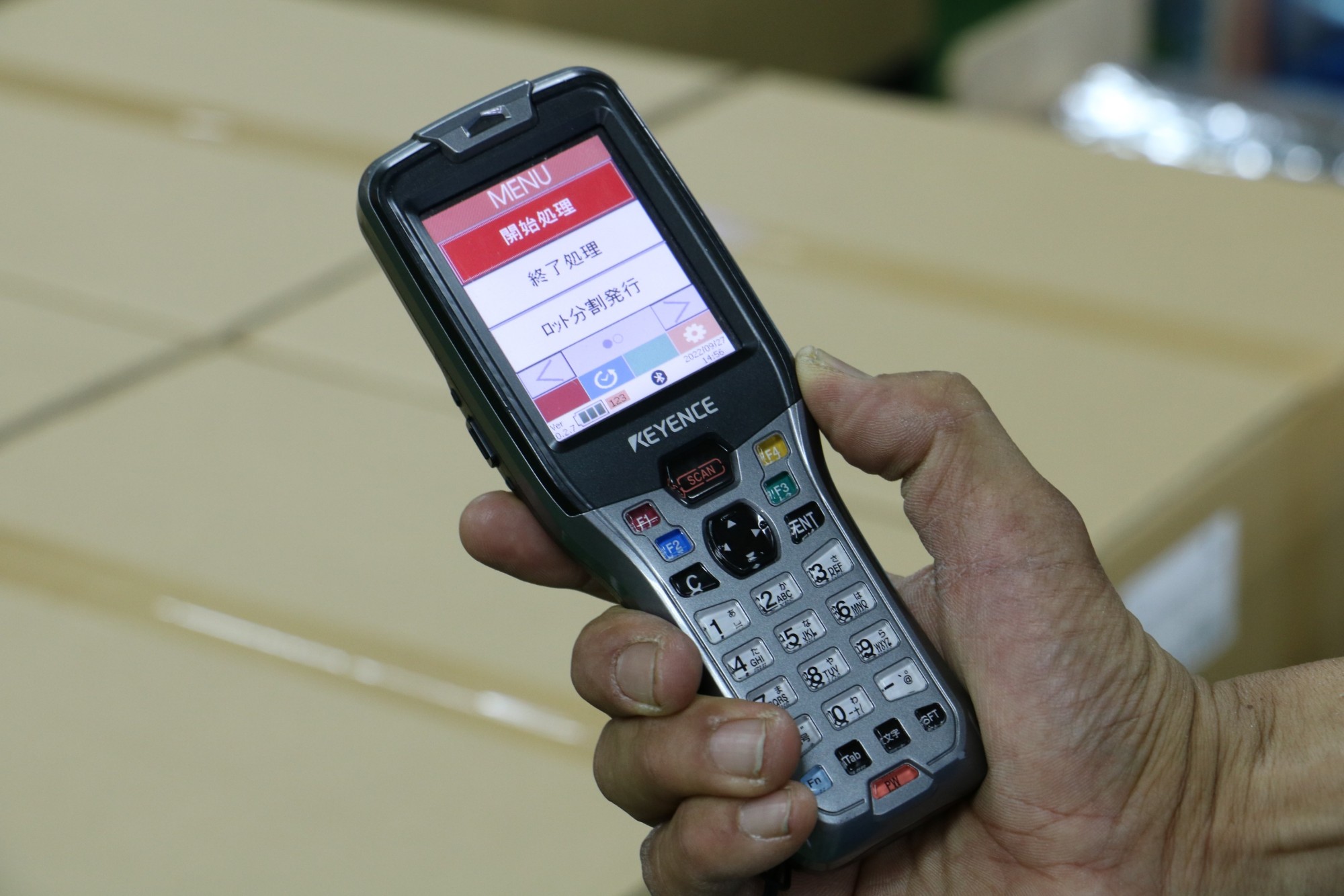
誰でも簡単に使えるシステムが、顧客に信頼されるデータ管理を実現
---システムの導入後、どのような効果がありましたか??
以前はアナログで記録したデータをExcelに打ち込み直す作業をしていたのですが、それがなくなり管理側の業務短縮になりました。現場では新しくバーコードを読み取る作業が追加されましたが、難しい操作が必要ないので安定して稼働しています。
そしてデジタル管理になったことで、お客様の信頼も得られるようになりました。作業時間が把握できていることで、納期について正確な回答ができ、データがあるからこそお客様に納得していただけています。
ハード面については、さまざまなスタッフがハンディターミナルを使うため、誰でも使えるような操作画面にしてほしいとお願いしていました。依頼どおり一連の操作がわかりやすく設定されており、文字も大きくて見やすいので、万人にやさしいシステムになりました。現場での操作ミスは出ておらず順調に使用できています。
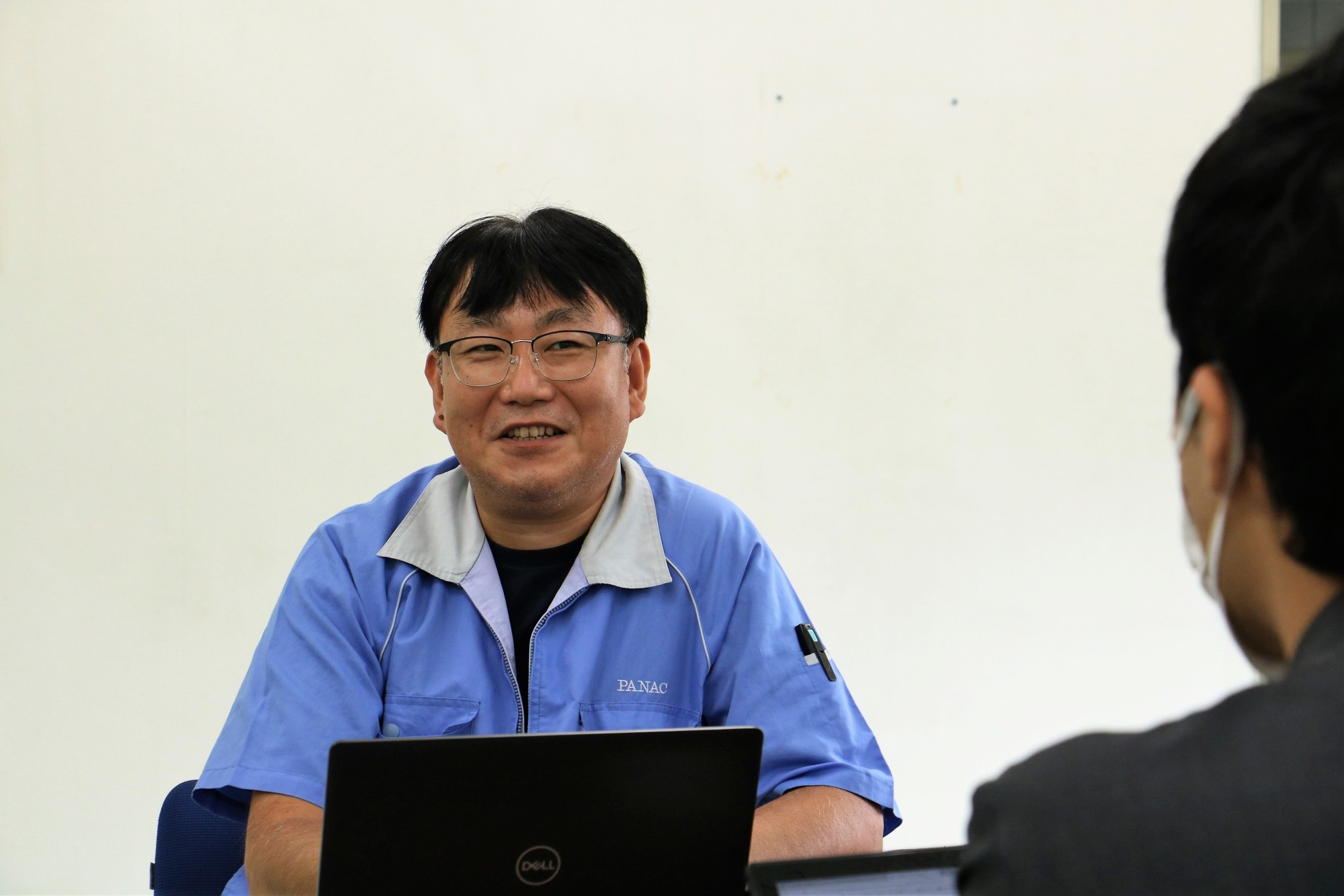
人の手管理からデジタル管理へのシフトチェンジへ
---初期導入後の展開と、今後の展望について教えてください。
最初のステップでまずは亀山工場にシステム導入し問題なく運用ができることが確認できたので、次のステップで同じシステムの他拠点展開を行いました。システム自体は必要最低限の機能をもったシンプルな構造にしてもらったことで、簡単なマニュアル作りをして拠点に渡すだけのスムーズな展開ができました。
この工程管理をはじめ、今後も在庫管理や出荷管理などのあらゆる作業データを収集できる管理体制を整えて、お客様の安心につなげていきたいと思っています。
社内の業務簡素化にも目を向けており、人の手で管理していたものをデジタル化すると、人手不足などの課題にも寄与することになるので、少しずつデータ活用の歩みを進めていきたいです。
---パナック様、取材のご協力ありがとうございました!